28 January 2020
Ask an apprentice: Luke Bailey
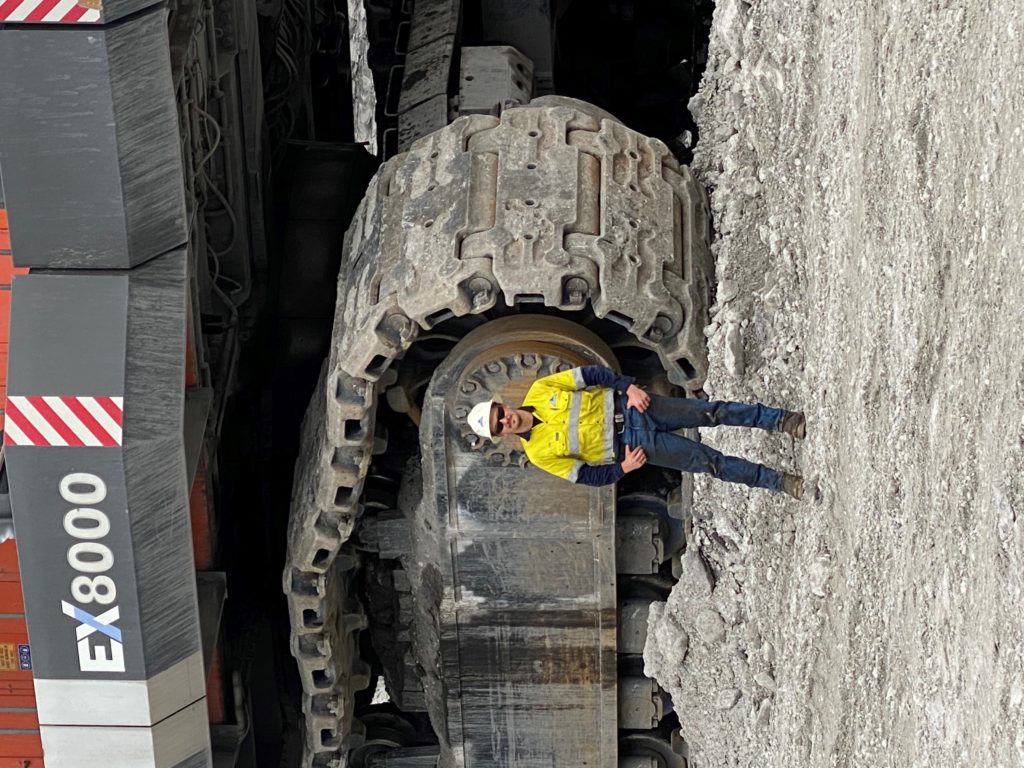
We recently spoke with Luke Bailey, a Mobile Plant Mechanic at the Maules Creek Coal Mine, about his experience completing an apprenticeship with Whitehaven.
Tell us a bit about yourself: I was born and raised in Narrabri, I always had an interest in the mining industry and in cars, and knew I wanted to stay in the area.
Why did you do an apprenticeship? I always knew I wanted to work rather than go to university. I was interested in cars and my family was orientated around mechanics, but I didn’t necessarily want to work only on cars for a job. I saw a position advertised in the local paper for a school based apprenticeship with Whitehaven’s Maules Creek mine, and I thought it’d be interesting to work on gear like trucks and diggers that you don’t usually come across every day.
What did your apprenticeship involve? From Year 11 I started doing three days a week at school, one day at TAFE, and one day at work. Back then, the mine was still under construction so I started working at a local road transport workshop to get experience. I finished Year 12 as a second year mobile plant mechanic apprentice and a few months later I was offered a role on site.
I started at Maules Creek in 2015 and there were only 9 trucks and 2 diggers, now we’ve got about 70 trucks and 10 diggers. I started off in the workshop and was on a shift rotation. Back then we had four crews who rotated around the clock. During my apprenticeship, every 8 to 10 weeks I’d go to Tamworth TAFE for a week and I did that for about three years.
All up my apprenticeship was two years during school and three years on site, and I’ve been fully qualified for two years now. Since then I’ve gone back to TAFE and got qualifications in road transport mechanics and to repair aircon in vehicles.
Describe a typical day: I’m now on the digger crew, so not on shift rotation anymore. At 5.15am, I’ll be there with the supervisor and leading hand of my crew to do a handover from the night shift. It’s our job to collect all the parts and sort out all the tools that we need for the jobs that day. Then we get down into the pit and do whatever’s in the plan for that day, which can range from day-to-day servicing, to diagnostics, to replacing components and engines.
What’s been the biggest surprise? In mining you’re working on a lot of the same equipment, but I didn’t expect that the company would be happy to send me off site to get more experience. They sent me to one of our engineering suppliers out in Orange to rebuild engines sent from our site, and I did 8 weeks in Singleton working on a grader rebuild. They’ve also put me through a supervisor’s course so I can start learning to manage people and plan work for each day. Day to day though I’m on a good crew and I enjoy what I do.
How did you find the transition to full-time work? I used to work on weekends and during free periods, so going to work wasn’t too much of a change for me. The biggest thing was learning the mining slang – like when I got the phone call to go on site and I was told to bring my crib bag but I didn’t even know what crib was.
Do you have any advice for people still in school who might be thinking about what to do for a career? I’ve always believed you don’t need to go to university to get a good job, because everyone needs trades as much as any other type of role. University’s not suited for everybody, and if you’re interested in pulling things apart and wanting to know how stuff works then mechanics might be for you.
Back to News